Rust Repair
#27
Originally Posted by thetremendousti
My friend said he will let me borrow his mig welder tomorrow, and some cutters, so I am thinking about and buying some 3/16" stainless steel sheets at Lowe's. Should I just dive in? Any tips? I've been searching and reading forums on hybrid and zcar and obviously here so...
I'm really just pointing this out in hopes that someone who knows will say:
Yes, it will be fine
or
No, don't use stainless steel
#28
^^^ Yes, you can weld normal to stainless, but the two steels have diff melting points and the weld will still corrode unless you use a stainless steel wire. It's not recommended welding the two types together.
Thetremendousti... Body & sheet metal work isn't just something you can do w/o any knowledge. Would you want a doctor w/ no medical knowledge to operate on you? Why not?
Because he's going to do more damage than good.
If you want to repair your car, the best way to learn is to take Auto Collision Repair classes. If that just isn't an option, read a bunch of good auto body books.
Lastly, rust repair IS NOT EASY. Cutting out the panels is usually the best way to go, but then you either need to get a replacement panel, or fab one up. And believe me (I did body work for years) that fabbing up a replacement panel will make you want to punch the wall until you really get the hang of it.
Long story short... Obtain LOTS of knowledge before doing body work. AND!!! do not start on your Z... get a beat up clunker to practice on, because you WILL screw up the first few times.
Thetremendousti... Body & sheet metal work isn't just something you can do w/o any knowledge. Would you want a doctor w/ no medical knowledge to operate on you? Why not?

If you want to repair your car, the best way to learn is to take Auto Collision Repair classes. If that just isn't an option, read a bunch of good auto body books.
Lastly, rust repair IS NOT EASY. Cutting out the panels is usually the best way to go, but then you either need to get a replacement panel, or fab one up. And believe me (I did body work for years) that fabbing up a replacement panel will make you want to punch the wall until you really get the hang of it.
Long story short... Obtain LOTS of knowledge before doing body work. AND!!! do not start on your Z... get a beat up clunker to practice on, because you WILL screw up the first few times.
#29
Alright, A few questions.
Today I took to grinding the hatch area to get rid of the rust and paint and did so, mostly successfully (see pics).
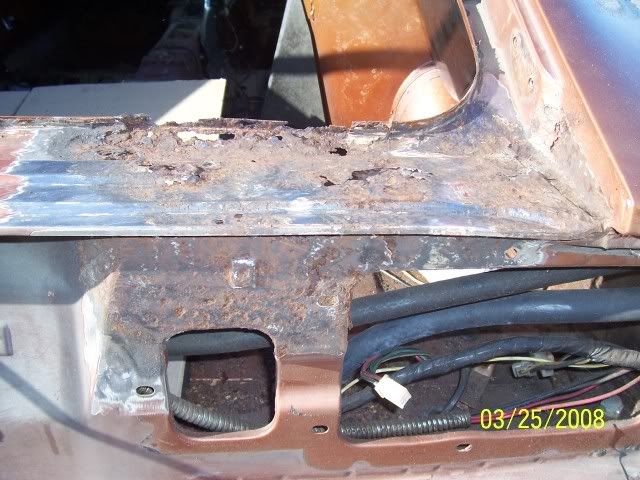
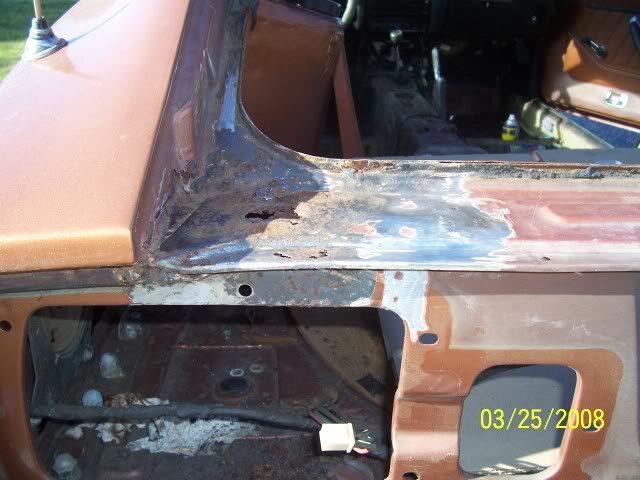
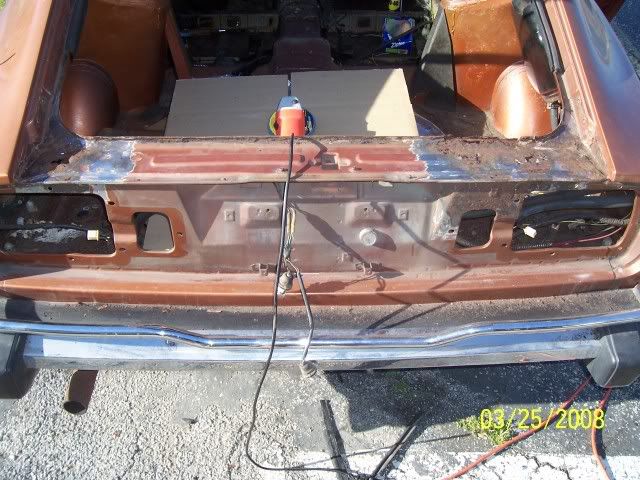
Then I took up the carpet and found a bunch of panels that have the consistency of tar and they are "glued" or more plainly "stuck" to the panels, so I took a chisel and after like 2 hours got some of it off and ground to the bare metal. What is this stuff?!?!? (see pics)
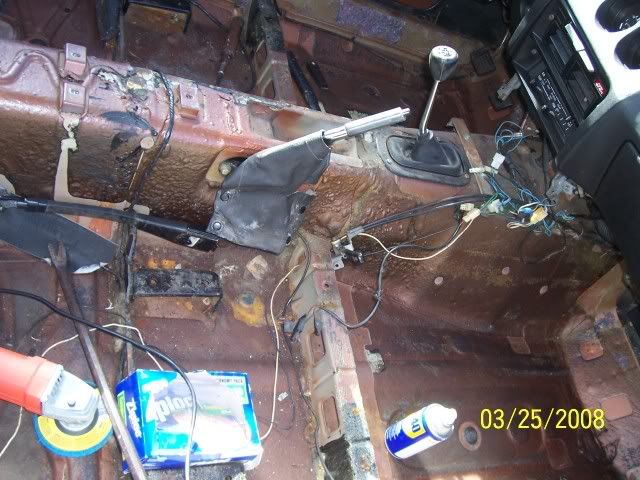
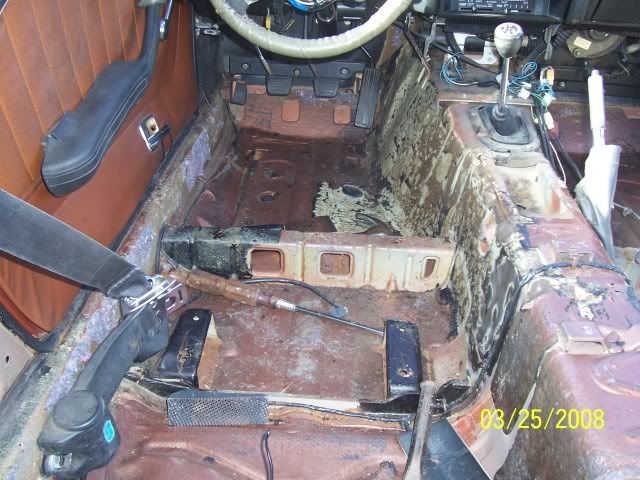
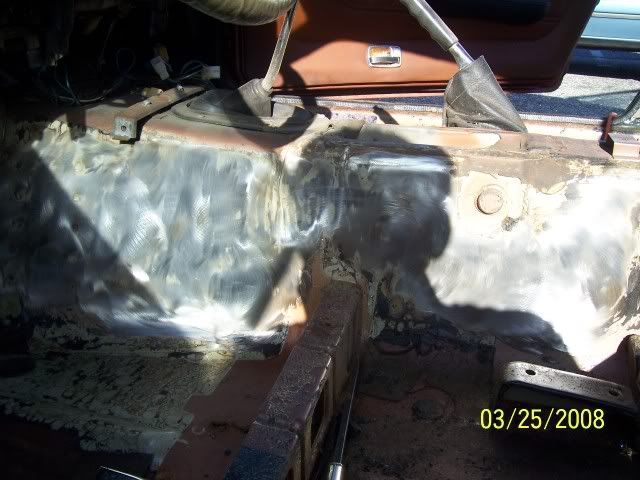
Finally, I bought some 26 gauge sheet metal and this guy I know said he'll sell me his mig welder. It's an Easy Mig 100 and here are the specs
*90 amp flux wire
*120v/60HZ
*31V Adjustment Positions: 2 Steps Range of current 50-80amp Duty Cycle: 15%@80A; 20%@65A;
Rated duty cycle: 10%@90amps Insulation Class: F Welding wire size:.035" to 040"
Can i use .03" wire to weld the 26 gauge steel to the body? If not what gauge and wire should I use for the body?? I have a friend that welds and he usually uses an arc welder which he let me borrow but it pretty much burns through all my practice metal.
Today I took to grinding the hatch area to get rid of the rust and paint and did so, mostly successfully (see pics).
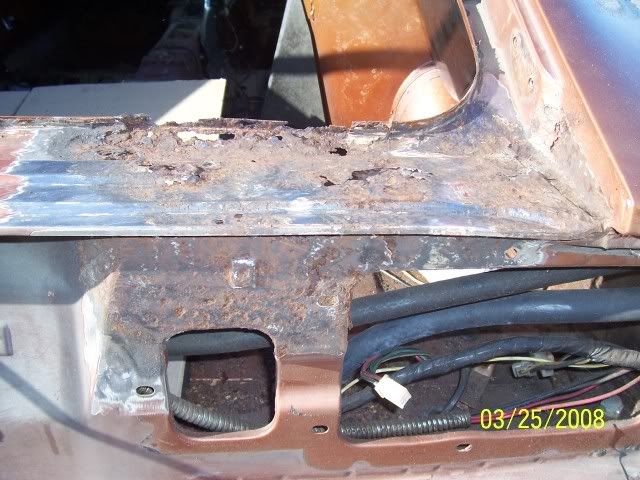
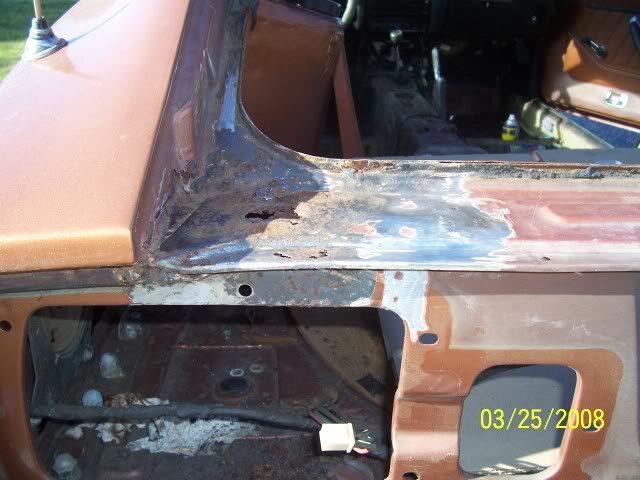
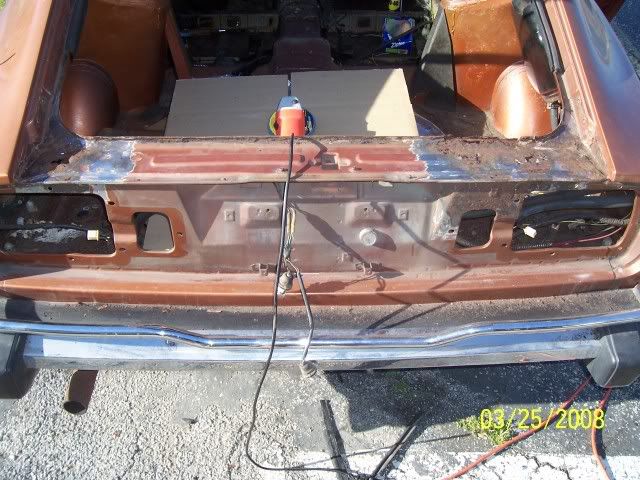
Then I took up the carpet and found a bunch of panels that have the consistency of tar and they are "glued" or more plainly "stuck" to the panels, so I took a chisel and after like 2 hours got some of it off and ground to the bare metal. What is this stuff?!?!? (see pics)
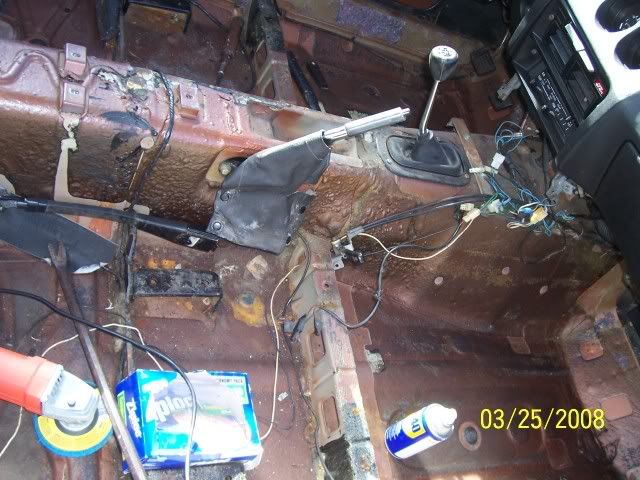
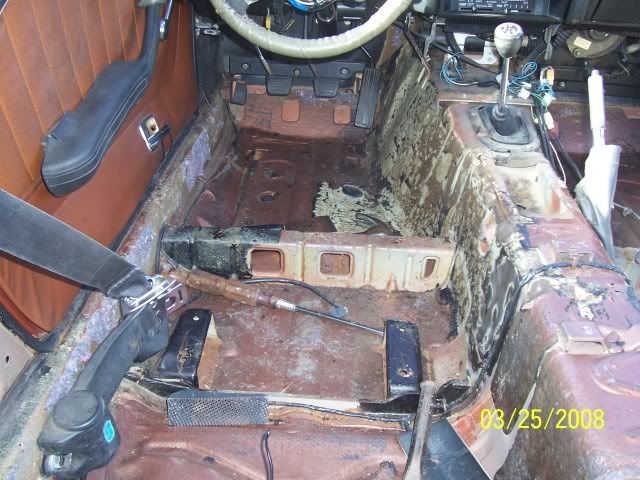
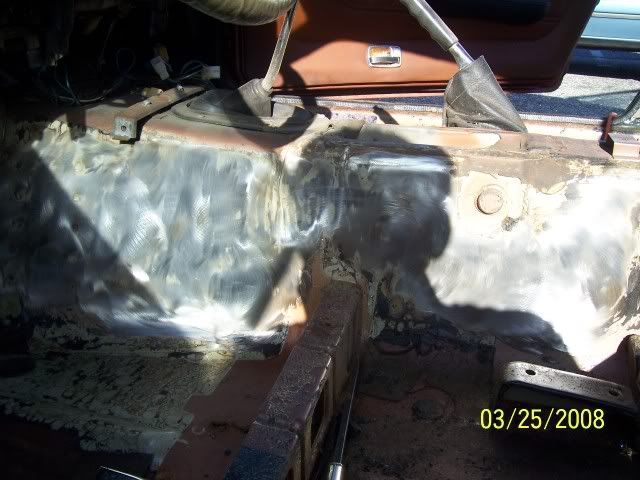
Finally, I bought some 26 gauge sheet metal and this guy I know said he'll sell me his mig welder. It's an Easy Mig 100 and here are the specs
*90 amp flux wire
*120v/60HZ
*31V Adjustment Positions: 2 Steps Range of current 50-80amp Duty Cycle: 15%@80A; 20%@65A;
Rated duty cycle: 10%@90amps Insulation Class: F Welding wire size:.035" to 040"
Can i use .03" wire to weld the 26 gauge steel to the body? If not what gauge and wire should I use for the body?? I have a friend that welds and he usually uses an arc welder which he let me borrow but it pretty much burns through all my practice metal.
#30
Originally Posted by thetremendousti
Alright, A few questions.
Then I took up the carpet and found a bunch of panels that have the consistency of tar and they are "glued" or more plainly "stuck" to the panels, so I took a chisel and after like 2 hours got some of it off and ground to the bare metal. What is this stuff?!?!? (see pics)
Then I took up the carpet and found a bunch of panels that have the consistency of tar and they are "glued" or more plainly "stuck" to the panels, so I took a chisel and after like 2 hours got some of it off and ground to the bare metal. What is this stuff?!?!? (see pics)
Finally, I bought some 26 gauge sheet metal and this guy I know said he'll sell me his mig welder. It's an Easy Mig 100 and here are the specs
*90 amp flux wire
*120v/60HZ
*31V Adjustment Positions: 2 Steps Range of current 50-80amp Duty Cycle: 15%@80A; 20%@65A;
Rated duty cycle: 10%@90amps Insulation Class: F Welding wire size:.035" to 040"
*90 amp flux wire
*120v/60HZ
*31V Adjustment Positions: 2 Steps Range of current 50-80amp Duty Cycle: 15%@80A; 20%@65A;
Rated duty cycle: 10%@90amps Insulation Class: F Welding wire size:.035" to 040"
Can i use .03" wire to weld the 26 gauge steel to the body? If not what gauge and wire should I use for the body?? I have a friend that welds and he usually uses an arc welder which he let me borrow but it pretty much burns through all my practice metal.
Good luck.
LWW
#31
Safety first, never put a grinder down face down like that. Just looking out for you bud...
26 gauge is too thin. Try 18 gauge. You can cut it easily with a thin blade on your grinder or a sawzall.
Flux core wire sucks. I mean, you can do it... but it burns a little hotter than a true MIG process and will give you trouble when learning. Hopefully your buddy's MIG you're borrowing is better.
3/16" stainless is much too thick, and stainless isn't the proper material here for the repair.
You should go to a junk yard or autobody shop and pick up some old fenders, door skins, and hoods that you can cut pieces out of. It will also give you plenty of material to practice with.
To make the repair you're showing in the pictures, you'd want to make two or more pieces. At least one for the sill plate, and one for the vertical tail light panel. You can use cereal box cardboard to make your templates. Trim with scissors till its right, then cut it out of steel.
Good luck, keep us posted, especially if you have more specific questions.
26 gauge is too thin. Try 18 gauge. You can cut it easily with a thin blade on your grinder or a sawzall.
Flux core wire sucks. I mean, you can do it... but it burns a little hotter than a true MIG process and will give you trouble when learning. Hopefully your buddy's MIG you're borrowing is better.
3/16" stainless is much too thick, and stainless isn't the proper material here for the repair.
You should go to a junk yard or autobody shop and pick up some old fenders, door skins, and hoods that you can cut pieces out of. It will also give you plenty of material to practice with.
To make the repair you're showing in the pictures, you'd want to make two or more pieces. At least one for the sill plate, and one for the vertical tail light panel. You can use cereal box cardboard to make your templates. Trim with scissors till its right, then cut it out of steel.
Good luck, keep us posted, especially if you have more specific questions.
#32
Originally Posted by lww
That's what sound insulation consisted of back in the 70's! Dry ice is your friend.
.030 is a little thick for welding this kind of sheet metal. You want to use the thinnest wire you can so your welder doesn't have to use as much heat to melt the wire. If you have to "overheat" the wire to get it to melt, you're more likely to burn holes in your sheet metal.
LWW
.030 is a little thick for welding this kind of sheet metal. You want to use the thinnest wire you can so your welder doesn't have to use as much heat to melt the wire. If you have to "overheat" the wire to get it to melt, you're more likely to burn holes in your sheet metal.
LWW
Last edited by thetremendousti; 03-26-2008 at 02:07 PM.
#37
well this next question is a 4 parter..flux core or not and what's the going opinion on gas? is it worth it?..does it make the welds all that much cleaner? I mean i used to use this flux core hobart at the shop and it did a good job for being a 115v welder but i wasn't doing body work, i was welding trailers..c channel to c channel and what not..nothing as fine as body sheet metal.
#38
Read this thread: https://www.zdriver.com/forums/showt...ghlight=welder
#40
Hey I'm Using Flux core wire with a cheapie little easy mig 100 from miller welding it cost me like 125 for the machine and 2 feet of wire from sim's and it's working fantastically! Granted I've been practicing all day yesterday and since like 9 this morning but I'm getting the hang of it. I've been practicing on a hood I got down at the salvage yard and I finally got the setting. It's harder and there's definately alot more spatter and tons more sanding but it's working like a charm!
#41
Alright so i spent pretty much all of today fabricating these. What do you think of the joints for the two corner pieces? I practiced alot on a hood i picked up from the junkyard and then I just decided to use it. My hand is still vibrating from the grinder.
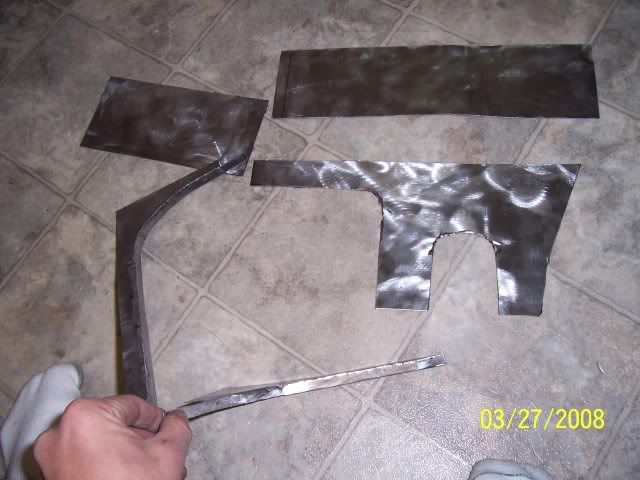
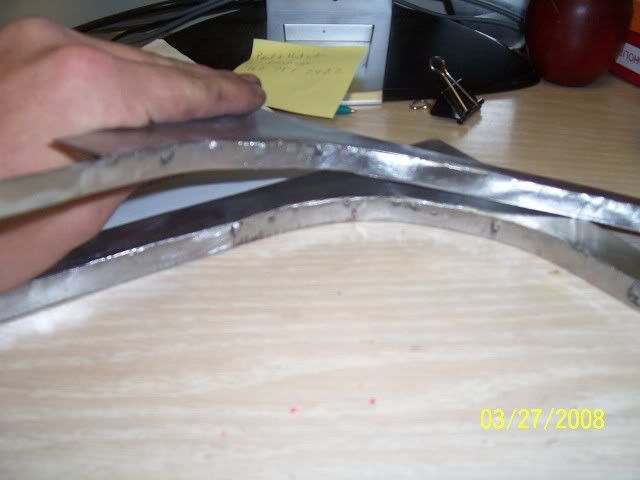
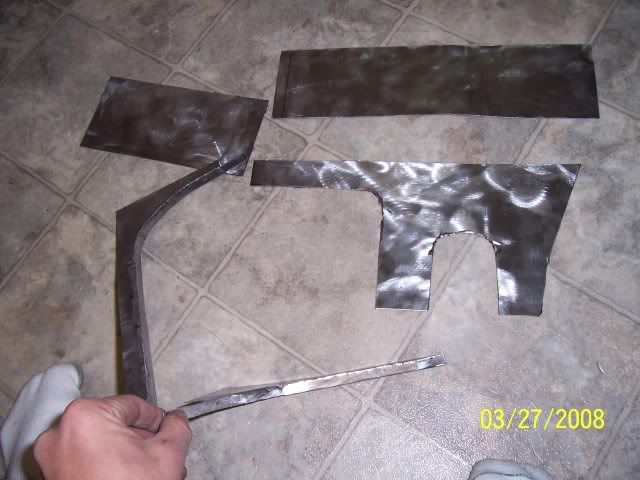
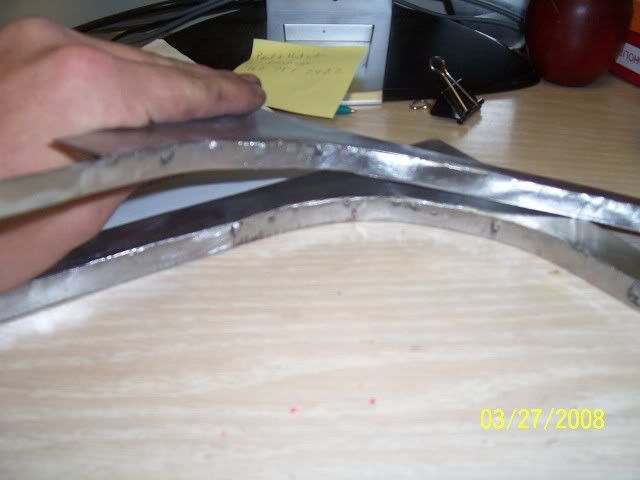
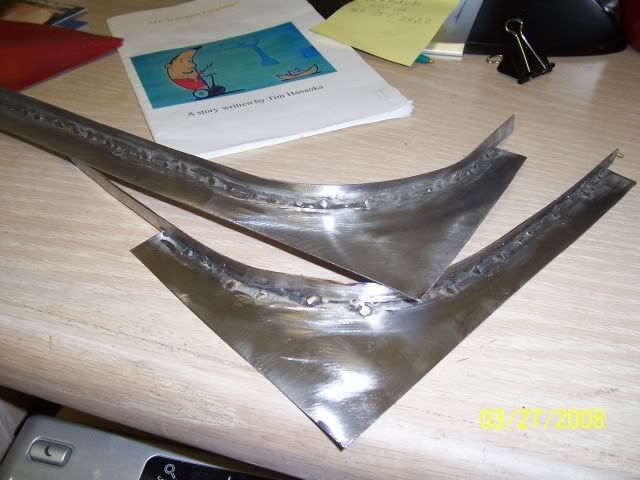
Thread
Thread Starter
Forum
Replies
Last Post
GNRick
280ZX Appearance Exterior, Interior
6
07-08-2014 09:14 PM
LeX
240Z, 260Z, 280Z Appearance Exterior, Interior
2
01-08-2008 02:03 PM
master300zx
FS: 240Z,260Z,280Z & 280ZX (70-83)
0
04-10-2006 08:50 PM
Bookmarks